COMPRESSOR ASSESSMENT: A student assesses the equipment on a job site. Emerson recommends that end users consult with their contractors to make sure their system is operating as efficiently as possible before considering the replacement of any compressor.
Compressors are the heart of any commercial refrigeration system, working tirelessly, day in and day out, in order to help end users keep their perishable items fresh in all types of applications, including supermarkets, convenience stores, walk-in coolers and freezers, and refrigerated warehouses. As such, they use a lot of energy, and as they age, they tend to lose efficiency, which is why replacing them with new, energy-efficient models may make sense for certain applications. Water Cooler Compressor
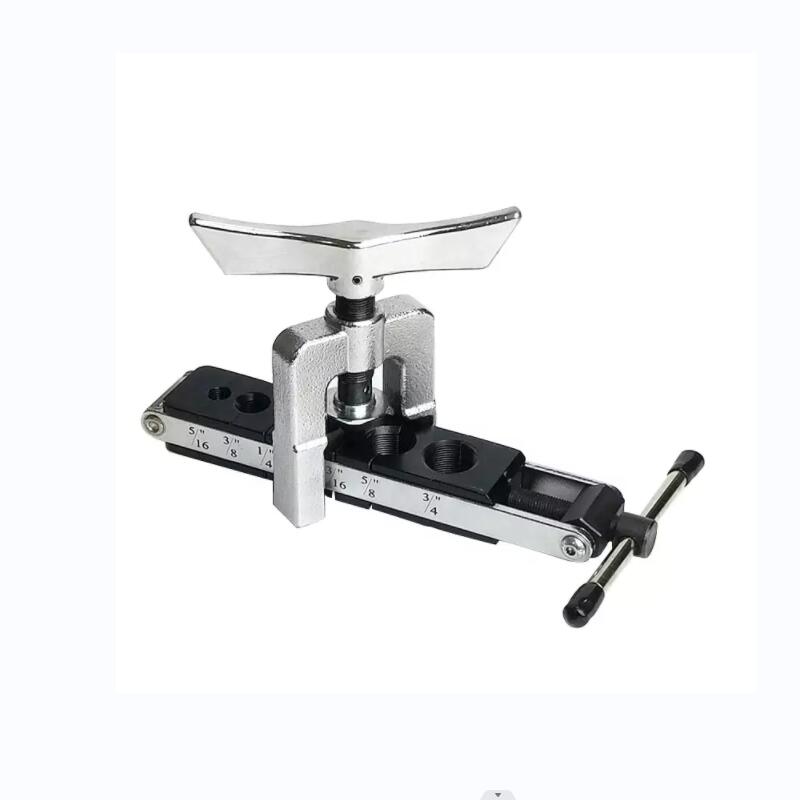
However, convincing end users to replace compressors that have not yet failed may be a difficult task, which is why contractors should first confirm that it is the correct decision for their customers to make. Recommissioning a system can help determine whether a compressor replacement makes sense, or if the money would be better spent towards replacing the whole system.
Operators often forget that over time, their refrigeration system steadily drifts from its original commissioned performance baselines, said Andre Patenaude, director of solutions integration, cold chain at Emerson. That is why they should consult with their contractor to make sure the system is operating as efficiently as possible before considering the replacement of any compressor.
“The decision to replace a compressor must be evaluated from a holistic assessment of the refrigeration system, and a key initial step of this process is to recommission the system,” he said. “And if the owner/operator wants to qualify for an energy incentive program — one that provides rebates for replacing inefficient equipment with newer, energy-efficient models — then they should also implement a formal measurement and verification (M&V) program in tandem with the recommissioning process.”
In a rack system, the next step after recommissioning should be to retrofit both low- and medium-temperature racks to enable a variable-capacity compression strategy for maximum energy efficiencies — either by upgrading to a digitally modulated compressor or adding a variable frequency drive (VFD), said Patenaude. He added that the best candidate for replacement is often a fixed-capacity compressor that is either underperforming or is the smallest displacement compressor in each rack. Replacing even one of these underperforming, fixed-capacity compressors with a variable-capacity digital compressor can result in significant benefits (see sidebar).
“Whether you’re using a digital compressor or adding a VFD to a fixed-capacity compressor, there are many advantages to being able to modulate capacity, including precise matching of capacity to changing refrigeration loads, improved case temperature precision, reduced compressor cycling (on/off), and tight control over suction manifold pressures,” he said. “All of these factors can significantly improve refrigeration system performance, energy efficiency, lifespan, and overall reliability.”
Contractors may be unaware that it is possible to add a VFD to a number of legacy Copeland Discus and Copeland Scroll fixed-capacity compressors in order to achieve some of the benefits of variable-capacity compression, said Patenaude. However, if the decision is made to replace a fixed-capacity compressor with a digital compressor, for many systems, he recommends following these steps:
Replacing the compressors in a refrigeration system should also be considered when retrofitting to new lower-GWP refrigerants, such as R-448A or R-449A. That’s because there may be compatibility issues between the elastomers in the compressors and the new refrigerants, said Steve Holden, manager of application engineering at Carlyle Compressor.
“Generally speaking, these elastomers were designed to be compatible with either the original refrigerant/oil combination or the replacement refrigerant/oil; however, exposing these elastomers first to the original fluids and then to a replacement fluid can yield a different result,” he said. “In addition, the system’s operating history, including duration and severity of conditions, can play a factor in aging these elastomers, so the lower risk approach is to replace the compressors.”
In these situations, Carlyle’s general recommendation is to replace compressors that are more than 15 years old. Holden noted that around this age, compressors have reached a reasonable operating life expectancy, and the material compatibility risks at this — or any — age should be seriously considered before deciding to change fluids without changing the compressors. If end users decide not to upgrade compressors when changing refrigerants, then Carlyle recommends that they consult with both the equipment and refrigerant manufacturers and follow their retrofit guidelines.
It is important to remember that when replacing compressors during a refrigerant retrofit, the primary goal is ensuring material compatibility, not improving energy efficiency, said Holden. He added that if customers are concerned with energy efficiency, they should consider system improvements such as Carlyle’s pulse-width modulation or variable-speed unloading technologies, either of which can be added to existing racks.
“Improvements in unloading technology enables tighter control of the suction pressure in the rack, which reduces compressor starts and stops, providing more consistent system operating temperatures and improved compressor reliability,” he said. “The efficiency benefit from modulated capacity is that the suction pressure setpoints can be raised without impacting case temperatures. These higher suction pressure setpoints have a direct effect on reduced power consumption.”
When end users ask Bob Bazzoli, service manager at EMR Delaware Valley, whether they should consider replacing their compressors to improve energy efficiency, his answer is usually no.
“If you have a car that is running well, and the mechanic says that if you replace the engine, you will get better gas mileage, you would probably say, ‘no,’” he said. “It’s the same with refrigeration systems. It is better to save the money for upgrades and put it towards new equipment. Then, all of the components will be matched, and end users will receive the greatest return on their money.”
Bazzoli noted that new systems offer numerous benefits, including better energy efficiency, greener refrigerants, and increased reliability. In addition, they are usually quieter, smaller, and easier to service, and he believes customers will experience greater peace of mind by purchasing new equipment, rather than replacing components in an older system.
Denny Martin, technical service specialist and product manager at Embraco North America, agreed, noting that compressors are usually only replaced in order to make a system operational again, not to upgrade overall efficiency.
“When equipment owners want more efficiency, they may do a refrigerant retrofit using the same compressor but with a more environmentally friendly refrigerant,” he said. “Otherwise, I believe if they want better efficiency, they are buying new equipment that uses variable-capacity compressors and hydrocarbon refrigerants. It is illegal to retrofit hydrocarbon refrigerants into old equipment designed for HFC or HCFC refrigerants, which is why they need to invest in new equipment that is specifically designed for flammable refrigerants. In addition, they should get a better overall bang for their buck by installing new equipment.”
That being said, Martin noted that in larger systems, better efficiency may be gained through a compressor retrofit.
Patenaude agreed, noting that for owners of large centralized rack systems, replacing a compressor may make the most sense, particularly if the refrigeration system is demonstrating signs of stress — including excessive compressor cycling rates or suction pressure swings — or experiencing diminishing performance.
“Our Copeland Mobile app can help contractors select a replacement compressor that meets Emerson’s recommended guidelines,” he said. “In addition, our application engineers are always available to answer questions related to refrigeration system performance and help contractors assess retrofit opportunities.”
Emerson conducted a case study to verify the energy-saving upgrades performed at a 20-year-old, 45,000-square-foot retail store. In this study, recommissioning the system led to an 18 percent reduction in energy costs for the retailer. The retailer also netted an additional 4 percent energy improvement by replacing one fixed-capacity compressor on the low- and medium-temperature racks with a new compressor (before activating any digital modulation capabilities).
By engaging the new compressors’ digital modulation capabilities, the retailer achieved an additional 12 percent energy improvement. The 16 percent reduction in energy costs from replacing the compressors saved the retailer roughly $17,000 a year in energy costs. In addition, the energy improvements met qualifications for a local energy incentive program for the retailer.
See more articles from this issue here!
Joanna Turpin is a Senior Editor. She can be contacted at 248-786-1707 or joannaturpin@achrnews.com. Joanna has been with BNP Media since 1991, first heading up the company’s technical book division. She obtained her bachelor’s degree in English from the University of Washington and worked on her master’s degree in technical communication at Eastern Michigan University.
You must have JavaScript enabled to enjoy a limited number of articles over the next 30 days.
Sponsored Content is a special paid section where industry companies provide high quality, objective, non-commercial content around topics of interest to the ACHR News audience. All Sponsored Content is supplied by the advertising company. Interested in participating in our Sponsored Content section? Contact your local rep.
On Demand In this webinar, we go through the recent updates on R-290 natural refrigerant, and the impact it will have on the HVACR industry.
Copyright ©2023. All Rights Reserved BNP Media.
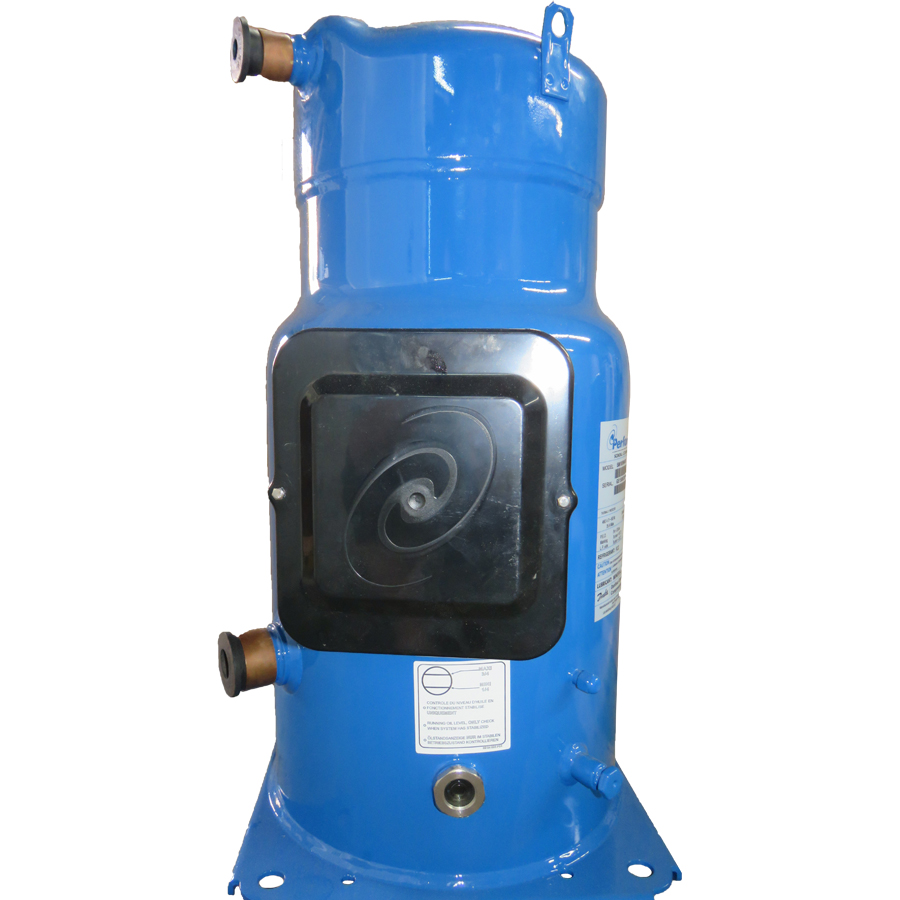
Two Stage Compressor Design, CMS, Hosting & Web Development :: ePublishing